Advances in the hydrogenation of biogenic TCR oils
The hydrogenation of bio-oils carried out by Fraunhofer Umsicht is part of the work package “Product Downstreaming” within the collaborative project Synergyfuels. In 2024, significant progress was made in hydrogenating thermo-catalytically reformed (TCR) bio-oil from sewage sludge, biowaste, and hop-spent grains. This has created important prerequisites for using these oils in the subsequent Synergy Fuels process routes. The results show that the various hydrogenated bio-oils can meet the quality requirements for fuels, such as diesel fuel, in accordance with DIN EN 590.
Approximately 200 liters of bio-oil were treated in total with variable hydrogenation parameters. The aim was to optimize the process conditions. The hydrogenation occurred at temperatures of up to 380 °C and pressures of up to 120 bar, with a continuous throughput of 0.5 liters of bio-oil per hour. During the catalytic conversion, both catalysts and process parameters were optimized. The activity, selectivity, productivity, and aging of the catalysts were taken into account. The results of the hydrotreatment were analytically measured using extensive online and offline methods.
Further optimization and commissioning
Further optimization and expansion of the pilot plant is planned for 2025. One focus will be on catalyst loading in order to further improve fuel quality. This will be done in collaboration with Clariant. At the same time, the process routes, including reaction control and reactor design, are to be further optimized.
A larger demonstration plant for hydrotreating biogenic oils will also be operated at Fraunhofer UMSICHT’s external site in Hohenburg. This plant will enable a throughput of up to 30 liters of oil per hour. With hydrogen pressures of up to 120 bar, process temperatures of up to 400 °C, and a H₂ throughput of up to 80,000 liters per hour, the plant offers extended possibilities for catalytic conversion, catalyst testing, and the production of significant quantities of products. This ensures the scale-up of the process route.
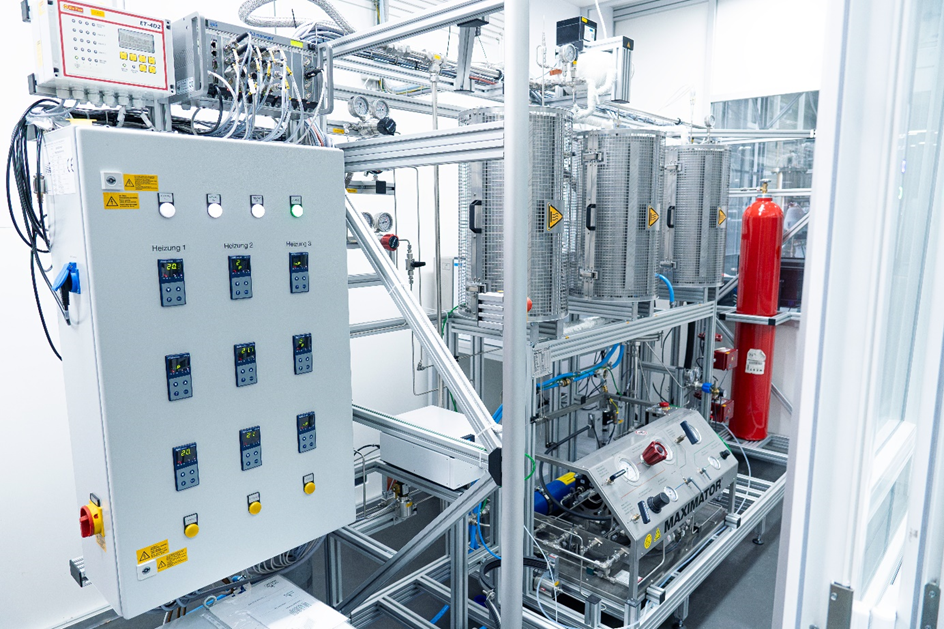
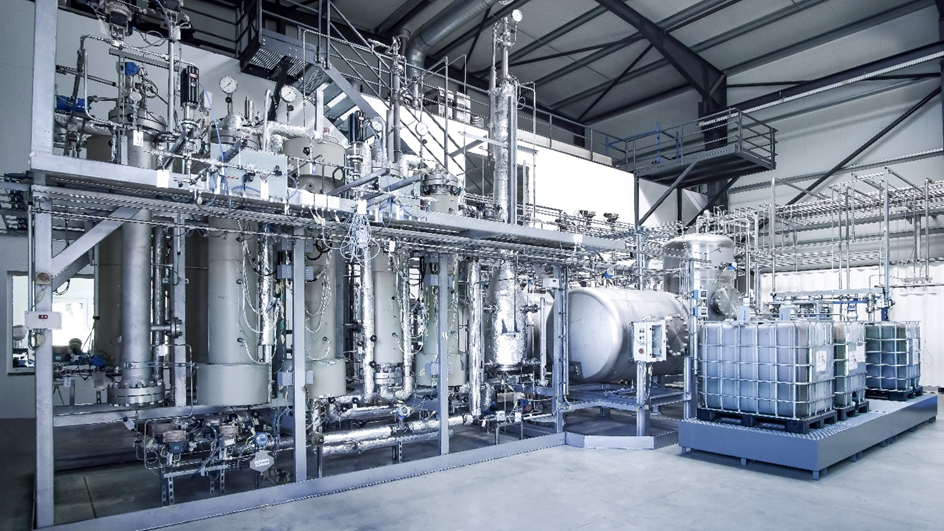